Introduction: Glass Fusing Control Test for Microwave Kiln
There is nothing more exciting for me than to come out with a perfect fuse. I am like a kid in a candy store when I am sharing my pieces of glass. I can tell from memory while driving down the road what colors went into the piece just glancing at it. I say this because, it has happened. I will be talking to someone and describe what went into every piece.
And that moment you lift the lid and you say Oh My Gawd, that is sooo pretty. Those are some pretty cool moments.
I am not just using the pieces that came with the kit anymore. I go to an art school in our region and pick out some of my glass. It gives me some great pieces but there is also some challenges with it. Some of this glass is textured with very different textures so firing times may be different than what you are used to. And to be honest per piece of jewelry I get out of it, I get it for cheap, I really like that.
This Instructable is how I tested the pieces from my last shopping trip. They were chosen for two reasons. One, I liked how they looked that is why I bought them and two, this Instructable.
I love fusing glass, it is a passion and with a microwave kiln, you can't manipulate it during firing or at least I haven't been brave enough to try yet.
So lets, just see what happened when I just played for the sake of playing, learned for the sake of learning and hopefully you can carry something away from it as well.
Step 1: Setting Up Your Controlled Test.
I have trouble fusing with a white base. When using white and firing it at the usual settings I use, I just kind of stand there and wait for the tink. Tinks are bad. Tinks mean that you are going to come out with a broken piece of glass or something you might can salvage with enough work at the grinding bench but you will not come out with what you thought it would so you got tinked.
So if we are going to explore, let's take the bull by the horns and use a white base for each and every test.
So the first thing I did was to cut kiln paper for each of the samples I was going to run. Then I cut the white glass base and laid it out on the kiln paper.
Can you tell I worked in Quality Control once upon a time? A controlled test equals all thing being relatively equal from beginning to end and the results speaking for themselves.
My method for testing was the same exacting firing time for each sample. Fire for One Minute, Rest for One Minute, Fire for One Minute, Rest for One Minute, Fire for One Minute and thirty second, allow to cool for Thirty Minutes and remove from the kiln.
These results were very interesting.
Step 2: The "Snake Skin" Pattern...
This pattern is very pretty but if you look at the close up picture, you can see that it looks almost scaly. This one was kind of and ironic purchase considering I had a black snake living in my house at the time of purchase. He has since been removed, so when we purchased this piece there was a little giggle at the fact that it looked like my house mate.
The result of firing this piece gave a beautiful result. The surface was smooth with the standard fusing time. The blue color in it dissipated and it seem like the green and black separated. There was no breakage at all. I was very happy. Couldn't get this one as a finished piece fast enough.
I was excited to see how this fused. I think the next time I fire this, it will be on black, just to see how that will look.
Step 3: The Semi Iridescent Piece...
In the close up, it almost looks like it glows, in the kiln pic, it looks a little flat, hence the word semi.
I had really hoped that this piece would turn out the way I hoped it would. With the blue having just enough sheen to it to make it really eye catching.
As it was firing, I was standing on the other side of my counter, the housemates last known whereabouts was in the kitchen so I fused from afar. I am a wise woman, I fuse from afar.
Then I heard the tink during the first rest period. That hurt my feelings a little but I finished the process. Kiln paper is some stinky stuff if you don't let it do it's thing. If you remove the kiln lid too soon, it give off some noxious fumes that will stink up your whole house, so word to the wise, don't take the lid off too soon.
Step 4: The Rippled Red Piece.
This pattern was akin to the snake skin look piece but it was different as well. As you can see in the first pic, the ripples are evident.
The first test went well so this one would surely go as well. When I am wrong I am wrong.
As you can see in the second pic, the red stayed in tact but the white could keep it together and it cracked. Not sure if this one is totally fixable but hey, I'll give it a shot.
Step 5: The Bumpy Green Piece.
As a person who like color and texture, I was excited to get this piece. When purchasing it, I was like feel this piece, you can feel the bumps on it. I had worked myself up into a frenzy about this piece, if the bumps didn't stay in tact, at least it should give me some cool effects.
Well, when fused it is a very pretty shade of green but it was as smooth as it could be. You would never know the bumps had been there. It was like they never happened.
The other odd thing about this is that the green broke this time. Notice the last pic, the white not only stayed in tact, it kind of swelled up in the middle just a bit, this may have cause the break in the green or been a result of it. I am really not sure.
Step 6: The Wavy Piece
Don't you just love the technical terms I use.
This piece was just waves of color. There was hints burgundy, brown, orange and blue. Some texture but not as much as some of the others.
I kind of thought that this one might tink but when I lifted the lid, it came out smooth with beautiful coloration.
Once again an excellent fuse.
Step 7: The Ruffled Red Piece...
Now I like red so I have lots of different reds. This one reminded me more of ruffles than ripped. It almost looks like it would be more fragile than the other red piece so I was, let's say doubtful that this fuse would turn out well, but I was in it to see what would happen.
So I pop it into the microwave and boy was I super happy with the result. It not only fused smooth as a baby's butt, it had some really cool let's call them ghost like etchings in it. It was so pretty.
Step 8: So There You Have It...
I am not saying this is the end all be all of microwave kiln test but it is a good way to start to play with your times. I am hoping to do another instructable about what I learned from playing with the times on these same pieces of glass.
If you try this and the glass breaks, it isn't the end of the world. Failure isn't fatal, it is a chance to learn and to do it better the next time.
If you have never tried microwave kiln glass fusing, I highly recommend it. It can give you hours of fun and you never know what you are going to get. It's kinda like opening a present every time you lift the lid.
Until next time,
Love, Peace and Cupcakes.
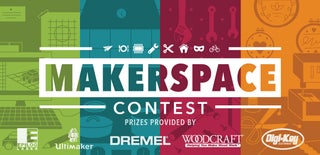
Participated in the
Makerspace Contest 2017