Introduction: Scrap Wood Ukulele Mosic Rosette
What to do with all the cutoffs from the maple, rosewood, mahogany, mango and other exotic woods. After a few years I got little pieces of wood coming out me ears. After seeing rosettes made by master luthier Beau Hannam I new what to do. I borrowed "stole" his idea !!!
Step 1: The Tools and Materials
Not much to it as far as the tools a router, a circle guide, a 1/4 " bit, a piece of plywood for a work board, a chisel, a protractor, double stick tape, stickpins, and sand paper.
Scrap wood cutoffs they came from back and sides already thickness sanded to 0.090 inches,
0.040 and 0.060 inch black white black purfling
thin super glue
Step 2: Lay Out on Plywood Workboard
I use old 3/4" plywood cabinet doors for a work board. I pick them up at thrift stores when I see them they are good for a lot of projects high ply count and for this it's nice to have the prefinished tops.
I go ahead and layout my sound hole and rosette lines on the board to make sure where I'm at when placing my wood pieces and purfling down.
I then put down the double stick tape in a large area around the drawn hole leaving the paper on except for area I'm working in, it helps keep the dust off the rest of the tape.
For the first piece of wood I find one or cut one with about a 10 degree angle on both sides. Lay it down on the ds tape making sure It's over the pre scribed lines.
Next I snip off a small piece of purfling push it up to the wood and fit my next piece of wood. Before I press it down to the ds tape put a little super glue on both sides of purfling. Jam the 3 pieces tight together and press down good to the tape.
Step 3: Getting Started
The first piece of wood I find or cut at about a 10 degree angle on both sides and press it down on the double stick tape across the lines I scribed before. Next I snip off a small piece of purfling (a laminated black white black strip of decorative wood used for guitar inlay) and my next piece of wood it doesn't really matter at this point what angle it is or how long it is as long as it covers the scribe lines. I do like to make some pieces of wood long to give more surface on the ds. tape. Before I press t down I put a little super glue on both sides of the purfling and push everything tight and press down on tape.As I go along I try to change angles at every joint. Some pieces of binding with pre attached purfling going long ways look nice with another piece on top.
Step 4: Keep If Straight and Flat
Use a planed flat block of wood covered in sandpaper to make sure your chisel cuts good and flat.
Step 5: Finish the Ring
As I lay in the cuts after every 3 or 4 pieces I coat the wood down with super glue. This keeps it together and also fills pours and any bad places. Keep it going the last piece might be a little tricky so take your time. After you're done coat several times with super glue letting it dry between coats.
Step 6: Route the Rings Out
I use a Jasper circle guide for routing the inner and outer circles. The guide calls for a 1/4" bit I use an up cut spiral bit. It makes a much smoother cut especially on spruce tops. The setup is simple for the rings it is layed out in 1/16" increments. There's a 1/8" centering pin you have to drill in your center point put it corresponding hole on the circle guide. I set the high hight of the of the bit to just cut though the wood and into the plywood maybe a 32nd of an inch
"Always test cut on a separate piece of plywood "
Cut both inner and outer circles and it's time binding
Step 7: Binding
I use 0.040" black white black guitar purfling( a thin laminated decorative wooden strip) pretty simple super glue and pushpins. I try to keep the binding up to the top of the wood it's a little bit easier to get the chisel under it when it's time to remove the rosette. I try to cut the ends so they will fit tight as I can but the fretboard is going to cover it up.
Step 8: Time to Remove the Rings From the Work Board
The best way I've found is to take a thin automotive feeler gauge and a blow drier. Take this step very slow you don't want to hurry through and break up all your hard work. I heat it and the feeler gauge at the same time as soon as the glue warms up enough it comes up pretty quick.
After you get it off I put something heavy on it and press it flat it gets kind of wappy jawed when you get it off the work board. Lastly with a piece of sandpaper knock off any excess glue on the edges and it's done
Step 9: Inlaying the Rosette
I use the same circle guide and bit to route the ukulele top. After setting up guide make a test cut on a scrap piece of plywood . It takes 2 passes to make route the channel wide enough for the rosette. I have a 0.095" top when I thickness sand it so I only cut the channel 0.060"s deep. After setting the rosette, gluing and clamping over night a few passes through the drum sander will flatten it down to the same as the top ready for thickness. that's about it just a little touch up and I'm moving on.
Thanks for looking hope you enjoyed this instructable and maybe it's helpful to you.
Ricky
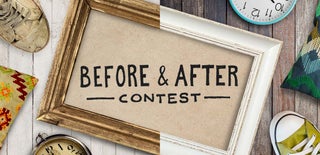
Participated in the
Before and After Contest 2017