Introduction: Antique Window Storage Cabinet
There are so many great items out there that you can find in places like yard sales, craigslist, Goodwill or FB marketplace - things that people might describe as "antique" or "scrap" or "reclaimed" or "cheap" - things that you can integrate into your work to create pieces that are both aesthetically pleasing and traditionally functional, as long as you're willing to do the legwork to connect the dots.
Such was the case in this project, where a coworker of mine came to me with an antique window that his wife came across at a yard sale. It was in fairly rough shape but he wanted to see if I could turn it into some sort of storage cabinet for their bathroom, which was in the process of being remodeled. I have a garage full of half-finished and "conceptually evolving" projects, but I'm always happy to use an excuse to procrastinate working on these and help a friend out with a project of their own. I'll get into the planning phase of the cabinet in a moment, but first a look at the materials and tools I used for this build:
------------------------------------------------
Materials Used:
Antique window
Pine boards for the cabinet body (I used a mix of 8" and 10" wide, 3/4" thick boards)
Cans of flat white spray paint
General purpose "quick" sealant / caulk (for the edges of the windows)
Wood glue and wood filler
Tools Used:
Table saw
Router with straight bit (for cutting dado slots - this is optional depending on your joinery preference)
Power drill & wood screws
Air compressor & brad nailer (optional)
Jigsaw (optional)
Random orbital sander
Clamps
Card scraper & chisel
Abrasive pad (see painting section for more info on this)
Step 1: Analyze, Planning and Initial Clean Up
Let's see what we have here. This window has all sorts of issues that we need to address before we get into the details of planning this build. As you can see from the pictures, there are several built in metal strips on the body of the window, as well as a host of staples, wire, tape, what looks to be hot glue, and a good amount of cracking paint and caulk-like sealant around the edges of the window. When dealing with any sort of antique that's been painted, a large concern that needs to be considered before any work is done is whether or not you may be dealing with lead paint. Needless to say, this is an issue that should absolutely be addressed, as I would highly suggest staying away from any sort of restoration job in which you encounter lead paint.
Usage of lead paint in housing was banned in 1978, but that doesn't mean you wont encounter it on pieces made decades on either side of this date. It's the deterioration of lead paint that is the concern, so any time you see an antique with cracking or peeling paint - buyer beware. Luckily, the are some products available at your local hardware store that can instantly reveal whether you are dealing with lead paint. While these won't indicate the level of lead on a surface, they can at least identify its presence. It's not a bad idea to have one of these kits with you if you're going to check out any reclaimed wood or antiques that you may use in your projects.
My window tested negative for lead, so I proceeded to strip all of the metal, glue, and sealant off of the window. Since the future owner of this cabinet was looking to "distress" the final product to help enhance the perception that it is a reclaimed piece, I wasn't overly concerned with sanding away the existing paint before getting to work on the rest of the build. With as clean of a slate as I needed, I moved on to constructing the body of the cabinet.
Step 2: Building the Cabinet
Obviously, every piece of reclaimed wood or antique you deal with will have it's own dimensions to consider, but I'll include mine here for reference. The door was 30 3/4" tall and 19 1/4" wide when I included the extra width of the hinges that I'll be using. To minimize the final weight of the cabinet - and since I will be painting the piece all white at the request of the client - I decided to use common pine boards for the body. I went with 3/4" boards to balance a lighter weight while ensuring enough structural integrity in the final product. I also wanted to have about 6" of useable storage space on the interior of the cabinet. Thus, I needed to cut my 3/4" boards to the following lengths/widths for the cabinet body and interior shelves:
31 x 7 3/8" (x2 - the sides)
20 3/4 x 7 3/8" (x1 - bottom)
22 1/4 x 7 3/8" (x1 - the top, which will have a 3/4" overhang on each side)
20 x 5 5/8" (x2 - the shelves, which will sit within 3/8" deep dado slots on each side piece)
With the pieces cut, I laid out and clamped down the two side boards and drew out where I wanted to cut my slots for the shelves, which I positioned to match the cross beams in the window. Of course, you can do simple butt joints and drill screws to hold the shelves, or use mounting hardware for the shelves to sit on, but a good dado joint is always my preferred choice in this case. Similarly, there are several options when cutting dados: a dado stack on your table saw, chisel cutting by hand, or using a straight bit on a router. I wanted to try out my new DeWalt Compact Router, and built a jig to make cutting these slots easier.
Measuring the distance from the edge of my 3/8" straight bit to the end of the router base, I knew my jigs needed to sit 2 11/16" from the outside of my slot edges. I secured these to my board with small brad nails, but some solid double sided tape will hold them against your workpiece as well (see pictures above for a better frame of reference). As I will be leaving about 2" of clearance between the edge of the shelf and the door, I indicated this on the slots and will stop my router bit right at this line. You can certainly use a plunge router if you have one, but for those who don't I used a forstner drill bit to cut a 3/4" hole 3/8" deep into my slots and started my router bit here. When cutting with your router facing down, always aim to move your bit counter clockwise - in other words, if pressing your router base against a jig toward your body, move the router body right. It won't take much of an effort to see which way the router wants to cut, so follow its lead.
After the slots are routed, clean up the corners and any edge tear-out with a chisel. Give your boards a thorough sanding before preparing to assemble the pieces together. Make sure your shelf pieces fit snugly in the slot, and then lay everything out to test fit the entire project before proceeding. A couple of my dado slots were just slightly wider than the board width of the shelves, so after gluing I filled these gaps in with wood filler and used a card scraper to clean up the excess.
Using a liberal amount of wood glue, I assembled the cabinet frame and clamped down the pieces. When I'm not using nice hardwood for a piece of furniture, I often shoot some small brad nails into the joints with my air compressor to help ensure that the fit will hold. And since this piece will be hung on the wall and filled with items, I wanted to use some wood screws to increase the rigidity of the cabinet. I drilled pilot holes and counter sunk the screw head positions before driving home some 2" wood screws in my butt joints on the top and bottom of the cabinet. Since this piece will be painted, I used some leftover wood filler to hide the countersunk screw head voids, and scraped the excess off with my card scraper. Once the glue and wood filler was totally dry, I sanded all of the joints down to ensure a super smooth transition between boards, and gave the assembled cabinet a final sanding to make sure all edges and corners were smooth.
One more test fit of the door, and I determined where I wanted to position my hinges. Once they were in place, I drew an outline to help guide their placement while I screwed them into the body of my cabinet.
Step 3: Prepping
Before I attach the door, I want to tape up all of the glass to prepare for my paint job. Using standard painter's tape I overlapped the strips, taking care to make sure the edges were perfectly placed. I then used an exacto knife to precisely trim the excess tape off of the other two edges. This process took some time, as I had to tape both the inside and outside of the six windows, but it's best to go slowly here and ensure that everything is prepped properly to minimize any clean up that you need to do after.
I then attached the door to the hinges prior to painting, and made sure that it fit perfectly (spoiler alert: it did!).
Step 4: Painting, Caulking, and Backing
Using cans of flat white spray paint, I applied two coats thoroughly over the entire piece: door, interior, exterior, hinges - everything. There are lots of options to protect the surface of the workbench you're painting on, but plastic trash bags ripped along the seams to a great job when only applying a thin coat like spray paint. I then let it sit for a day to dry and touched up any spots that needed another going over. ALWAYS use a respirator any time you are dealing with a product that's applied in a spray-on fashion, or any other substance that emits fumes. A cheap dusk mask is great for sawdust and sanding, but you need a real respirator for this type of work. They aren't overly pricey at the hardware store so do yourself a favor and invest in one. A tip when it comes to storing your respirator: after you apply some spray-on paint or finish, don't just take off your respirator and lay it down on your bench - keep it stored in another room that isn't full of fumes. This will increase the lifespan of your replaceable filters.
After fully dried, I used one of my Scotch-Brite abrasive pads to scrape away any rough or granular spots leftover from the spray paint. These pads are great for smoothing out a paint or clear coat finish without actually sanding away any of the surface - similar to how you might use steel wool. You can see from the photos how much dust these can remove to help smooth down your finish. After peeling off the painter's tape, I could see a few small spots where the paint made it through, but this can be removed with a scraper or chisel.
Now it's time for the caulking of the windows... I'll be the first to admit that caulking/sealing is not my strong suit, and this job was no exception. I just used some kitchen/bath quick sealant and rubbed my finger along the applied caulking, and you can see the results in the first picture... ug-ly. Thankfully this particular "quick seal" didn't harden for at least a half hour, so I had plenty of time to get my technique down. Rather than leave a thick bead of caulk along the edges, I took a rounded corner of my aforementioned card scraper and ran this along the edges, leaving a much thinner and less shameful end product. Once the sealant was finally fully dried, there were several smudges and uneven lines to clean up. Between my card scraper and a dull chisel, I was able to remove any excess caulk and straighten-up the lines of the sealant. Not perfect, but better. I smartly decided that repeating this process for the inside of the windows was not necessary, and moved on...
I wanted a thin backing for the cabinet that only needed to provide an aesthetic addition, as my coworker had another idea of how he wanted to mount it that wouldn't require any stability from the backing. I use tempered hardboard sheets as a top surface for all of my workbenches (it's scratch and fluid resistant, and also super cheap so I can easily replace the top surface of my benches whenever necessary), and had some extra sheets laying around. I traced the outline of the cabinet frame onto one of these sheets and cut it out with a jigsaw. After cleaning up these edges with 80 grit sandpaper, I spray painted what would be the interior side of the hardboard sheet with a couple coats of the same flat white paint.
To mount this onto the back of the cabinet, I wanted to ensure that there would be no gaps between the backing and the back face of the frame. I measured out where the shelves sat in the frame and noted this on the back side of the sheet. After clamping the backing in place, I used several 1 1/4" finishing nails to securely tack it together.
And that means that I'm....
Step 5: Clean Up and Finishing
...Almost finished. I went over the entire piece again with my abrasive pad to clean up any edges or rough spots. The client had a metal latch that he wanted to use for the door and I installed this before calling it finished. This was a fun project and the first type of cabinetry that I've attempted. I learn new lessons every time I take a stab at something I haven't done before (in this case, better methods for cutting dados, structural vs artistic decision making, and that I still have no skill with caulking...).
As always, I welcome any suggestions or criticisms about this build and design, and certainly let me know if you have any questions that I might be able to answer. I'd also appreciate your vote in the Before & After Contest at the ↑ top of the page ↑ - Happy building!
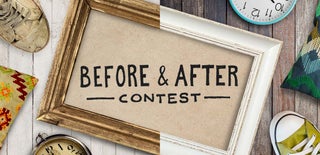
Participated in the
Before and After Contest 2017