Introduction: Adding a Power Lamp to a Stationary Tool
Knowing at a glance whether or not a tool is powered can be very important if you share a shop, have frequent shop visitors, Or just like to unplug everything at the end of the day.
This Instructable shows how I added just such a feature to one of the most dangerous tools in my shop.
Step 1: Gather Some Stuff.
You'll need some parts for this mod. I didn't use everything here, but gathered them together so you could get a general idea of stuff you might need for this kind of modification. Bear in m ind, If you're modding a new tool, you WILL void your warranty. But so what? You know what you're doing, And they should have put a power on lamp on it in the first place.
1: Drill and appropriate bits.
2: Screwdriver
3: Tape and Wirenuts
4: Lamp
5: crimp connectors and Crimping tool
6: Wire (Flexible multi conductor.)
Other useful stuff might be...
1: Heatshrink
2: Calipers
3: Wrenches (If the switch enclosure requires wrenches to disassemble)
4: Wire sleeving
5: Strain reliefs
Step 2: Pull Apart the Switch Mechanism.
I didn't include a photo because these vary from tool to tool. There's other ways to get power to your lamp, but the switch definitely has power running to it, and you need a guaranteed source that lets you know it has power whether it's switched on or not.
When you look at the switch mechanism, you really need to ask some questions:
1: is there enough room for the lamp I want to install?
2: How much wire do I need?
3: Where is a good place to put the lamp that is easily visible, but non intrusive?
Only once these questions are answered can you move on to the next step...
Step 3: Drilling For, and Installing the Lamp
I typically take the lens and bezel off and use them to lay out where I want the hole to be, but you can also use your calipers to measure from the edges to get the lamp perfectly centered or offset in a manner that looks best to you.
So, After you've marked it, take a very small drill bit and Pre-drill the center, Then the larger bit will follow the smaller hole.
Once it's drilled out, you can place the lamp and fix it in place, I do this with a rubber gasket. (Often the gaskets are included with these industrial lamps.)
Step 4: Wiring
This bit can be simple OR hard depending on switchbox layout, This old Craftsman saw had plenty of space for my wires, and I plan on another lighting project in the saw frame soon because of that.
White wires to white wires, and black to black. The ground isn't necessary for this lamp.
the neutral (White) is clamped in place with a wire clamp. This matches the original hookup, and will be durable if clamped properly. I recommend a ratcheting crimp tool for peace of mind.
The black wires need a different treatment, and the original type was not durable enough, so I chose a connector with a built in heat seal/shrink, A bit of heatshrink over the connector end prevents shorts in the unlikely event that it pulls loose from the switch.
Zip ties and/or electrical tape keep the wires neat.
Clampfor
The ends that go to the lamp require fork type connectors. Also with heatshrink, because double safe is good.
Step 5: Reassembly and Testing
Put the switch mechanism back together and make sure everything fits properly and that all wires will not snag on any moving part.
Once you've thoroughly inspected all moving parts that might touch the wires, you can plug in the tool and make sure your light comes on.
Switch on the tool and run through the motions making sure the light does not blind you (It doesn't.) but is still very visible.
Looking back from the door of the shop I can see the light well enough even with the sunlight streaming through the window.
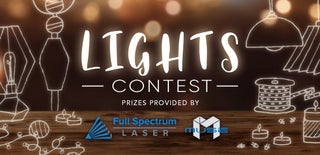
Participated in the
Lights Contest 2017