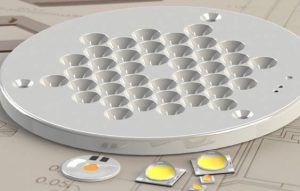
They deliver over 3000 lm in the beam from a unit 82mm in diameter and only 5.6mm – including optics, but excluding heatsink.
Key to including optics and LEDs in under 6mm of height is to use small die (~1mm) and surround each separate die its own reflector – which Plessey brands ‘Stellar’ technology.
The firm contrasts this with the CoB approach where multiple die share a single reflector – where the larger effective diameter of the CoB approach mandates a deeper reflector.
However, because the die have to be further apart to accomodate all the small reflectors, the Plessey approach means that its emitter has a larger diameter than a CoB with equivalent light output. Product manager Paul Drosihn told Electronics Weekly that this is an advantage when it comes to heatsinking as thermal contact area is increased – lending it to thin flat pancake-style luminaires – see diagram.
For luminaire makers, they can have one common type of heatsink and power supply, and to this attach which ever Stellar meets the beam width and colour temperature requirements.
Retail, industry, hospitality and outdoor lighting are foreseen applications.
Also on show was a device using similar Stellar miniature reflectors designed to show just how narrow the beam can be. Somewhat thicker than 6mm, this was a +/5° (10° FWHM) emitter of smaller diameter and lower output designed to fit an MR16 envelope – left in the picture with 82mm Orion on the right.
Plessey makes its own GaN-on-Si LEDs at its fab in in Devon.
Orion modules are not made in the UK, and Drosihn will not reveal where they are built, except to say it is not in China due to the risk of intellectual property theft – apparently Plessey has overcome considerable challenges in getting the x, y, z, and θ positioning precision required between die and reflectors for the mini-reflector approach to work.
He did reveal that the manufacturing site is automotive-qualified, opening the door to automotive products based on the technology.